Article
Q&A: ASTM B117 Salt Fog Testing
ASTM B117 salt fog or salt spray test is a very popular corrosion test designed to provide corrosion resistance information on metals and coated metals. The ASTM B117 test standard has also been approved for use by Department of Defense agencies.
Why should you consider running an ASTM B117 test?
- To compare the corrosive resistance of various metals or finishes
- To determine the corrosive tendency when a metal or coated surface is scratched (Perform ASTM B117 + ASTM D1654 together)
- To measure coating adhesion and corrosion creep (Perform ASTM B117+ ASTM D3359 together)
- To best estimate corrosion resistance in a marine environment (wetness, temperature, salt fog)
What results can you expect from a B117 Salt Fog Test?
与目视检查后B117腐蚀exposure, you can determine the suitability of coatings, paints and metals to resist corrosion or exposure to marine environments. With the addition of ASTM D3359 (adhesion with tape), you can see how well a coating adheres to metal and how far the corrosion crept. With the addition of ASTM D1654 (scribing), you can see how corrosion develops from a scratch through the paint or coating to the underlying metal.
It should be understood that correlating corrosive results from ASTM B117 exposure to real-world conditions is also not part of this test standard and is difficult to predict.
What deliverables does Element offer for ASTM B117?
Following an ASTM B117 test, Element will issue a test report, which will typically show:
- Photographs of the test samples. Pre & post exposure, or at any specified duration during the test. Many customers want a photo or the test to end at the first sign of corrosion.
- Calibration and compliance data of the salt fog chamber and supporting equipment.
- Detailed time/date entries of corrosive conditions, customer instructions.
- Element's accreditations, certification of test performed.
When is it not recommended to use ASTM B117?
Do not use ASTM B117 as the corrosion test standard when your product utilizes decorative chromium plate (nickel-chromium) on steel or zinc die castings or cadmium plate on steel. Use ASTM B368, Practice G85 for these materials.
What are the general conditions and most popular exposure durations of ASTM B117?
ASTM B117是体育rformed in specialized chambers built to ASTM B117 specifications. The temperature is maintained at 35C (+ 1.1C to 1.7C), with a pH range of 6.5 to 7.2pH and a salt atmosphere of 5 parts sodium chloride to 95 parts ASTM D1193 Type IV water, introduced into the chamber at specific air pressure guidelines.
ASTM B117 does not dictate the length of exposure. The standard calls for exposures in 24 hour blocks of time. The most popular durations are: #1) 96 hour exposure #2) 240 hour exposure #3) 600 hour exposure.
Additional Points to Consider when Specifying ASTM B117
- How Many Units To Test? B117 strongly recommends testing multiple samples at a time to help establish variability of the results.
- Product Orientation: How do you want test samples oriented in the chamber?
- Inspection and Photographs: Pre & post exposure, or at any specified duration during the test. Many customers want a photo or the test to end at the first sign of corrosion.
- Post Test Cleaning: B117 allows for specimens to be “gently washed in running water not warmer than 38C” – Most customers want Element to wash the part after the test and to before returning the part to the customer.
Element providesASTM B117 salt spray, salt fog testingas a rapid method to evaluate the corrosion resistance of your material, surface or coating.
For more information on our ASTM B117 testing services, or to speak to one of our Engaged Experts, pleasecontact us today.
View more articles aboutAerospace Testing ServicesFire and Building Products Testing ServicesInfrastructure Testing ServicesEnergy
Find related articles to you through theNucleus
providing CERTAINTY for nearly 190 years
More from Element
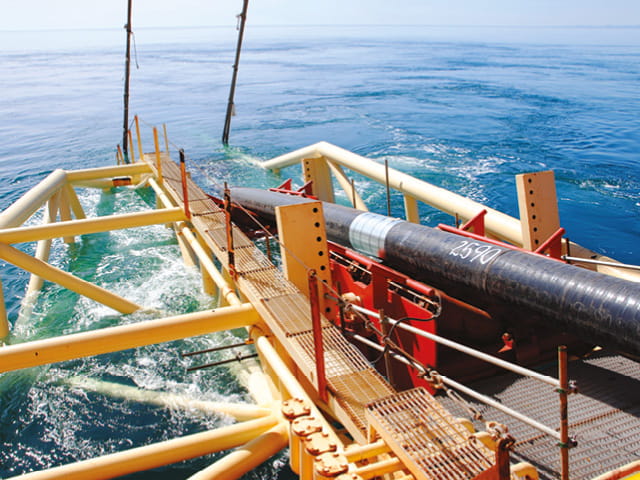
Coatings Testing
Find out about our Oil & Gas coatings testing services and how we help to make certain that materials, products and pipelines are protected from corrosion, ultraviolet light, water penetration, heat, abrasion and chemicals.
Read More
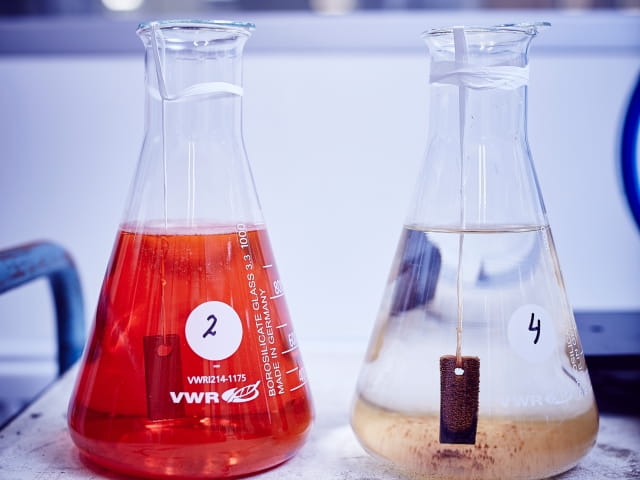
Corrosion Services
Find out about Elements extensive corrosion testing expertise in the Oil & Gas industry across a global network of laboratories.
Read More
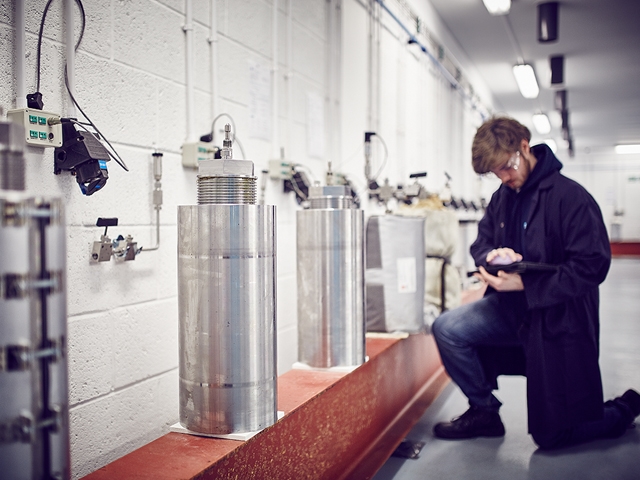
High Pressure High Temperature (HPHT) Exposure Testing Services
We offer extensive services for the qualification and compatibility of polymer materials exposed to production fluids at high pressure and high temperature (HPHT).
Read More
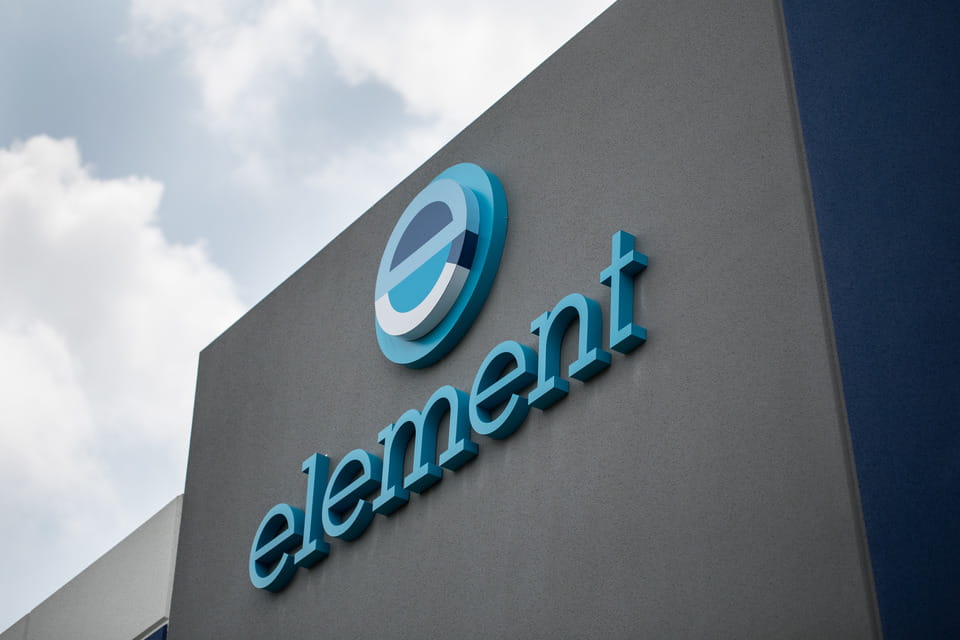
Local laboratories, global platform
Doing business with one of our laboratories enables our clients' access to our global platform of expertise, capacity and capabilities.
READ MORE
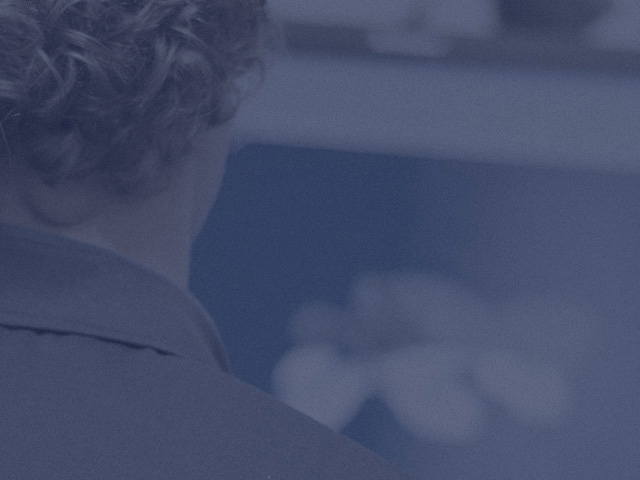